Structural Slab Crack Repair - Engineered Solutions For Commercial Strengthening
- Jarred Jones, P.E.
- Mar 30, 2024
- 3 min read
Updated: Apr 2, 2024
Amid the urgency posed by serious structural cracks, this comprehensive case study highlights Structural Reinforcement Solutions swift response to the delays plaguing a senior living facility's completion. With critical areas compromised and in need of structural slab crack repairs, occupancy was on hold and the urgency of the situation demanded an immediate and effective solution.
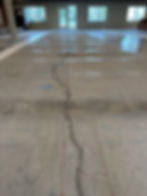

The awarded contractor for this critical repair leaned on SRS for essential material support, engineering expertise, and tailored training, enabling the seamless integration of carbon fiber reinforcement and the successful restoration of structural integrity in the senior living facility.
Surface preparation is critical for the successful installation of Fiber Reinforced Polymer (FRP) systems, particularly when dealing with high-strength concrete that is commonly used in commercial and industrial construction projects.


In this instance floor scarification was utilized to achieve the desired surface roughness of a CSP 4 on the top side of the slab. On the underside of the slab a diamond cup grinding wheel and dust extraction equipment was utilized to achieve a CSP 2. Bond testing was performed to confirm adequate results bonding to both the CSP-2 and CSP-4.



Due to gravity, the material flows downward and into the crack through the installed injection ports. The injection process is slow and controlled to ensure that the material fills the crack completely without creating air pockets, effectively bonding both sides of the broken slab together.
To ensure the safety and performance of the carbon fiber application, bond tests were performed to provide confirmation of the strength and reliability of the FRP system. In order to test the bond strength of the system, dolly's are epoxied to the surface of the FRP. Once cured, the FRP around the dolly is cut in order to isolate the pull-off test to a known area. The test is then carried out to confirm a failure in the substrate rather than in the bond to the substrate.
Throughout the test, various parameters are measured and recorded, including the applied force, the deformation or displacement of the FRP, and the corresponding strain. These data points help characterize the mechanical behavior of the carbon fiber bond. This analysis helps assess the effectiveness of the repair and ensures it meets the required specifications. In this case, due to the strength of the concrete being tested, the machine was maxed out at 3,500 psi and no failure was achieved.

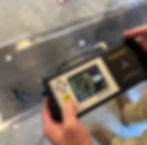
A controlled force is applied to the repaired area using aluminum dollies, gradually increasing until the structure reaches its breaking point or until the desired data is obtained. The force can be applied at a constant rate to measure the stress-strain relationship accurately.
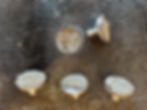
The results of the pull test are interpreted to confirm an adequate bond of the carbon fiber to the concrete substrate and made available immediately to share with the engineers of record on the project.

The ultra low-profile characteristic of the carbon fiber is of particular benefit in parking garage environments where clearance is limited, ensuring that structural repairs or reinforcements do not encroach on overhead clearances and existing mechanical installations.
Since Carbon fiber composites offer exceptional strength-to-weight ratios with minimal thickness, SRS-600 Unidirectional carbon fiber was specified to strengthen the cracked areas of the reinforced slab above the parking garage structure.

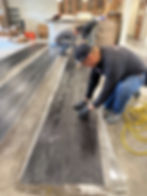
The primary purpose of the epoxy component of the system is to transfer loads between the concrete substrate and the carbon fiber. A strong bond ensures efficient load transfer, allowing the carbon fiber to effectively supplement the structural capacity of the concrete.

Fibrillated fibers or Cabosil was used to act as a thickening agent in the epoxy resin. When mixed with the SRS-1000 epoxy resin it creates a paste-like consistency that is effective for gap filling and bridging voids or irregularities in the substrate. This helps ensure intimate contact between the carbon fiber and the substrate, promoting adhesion and load transfer.
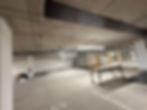

Compared to traditional reinforcement materials like steel, carbon fiber is significantly lighter. This lightweight characteristic minimizes the additional loads imposed on the structure. Additionally, it simplifies handling and installation, reducing labor costs and project timelines.
Overall, the use of FRP offers a permanent and efficient method for repairing cracks and strengthening structural slabs in parking garage environments, ensuring the safety and longevity of the structure for years to come. The dedicated support provided by SRS to address these pressing challenges head-on, ensured a and safe a completion of the project.
#carbonfiber #carbonfibre #CFRP #FRP #structuralengineering #structuralstrengthening #slabrepair #concreteslabcracks #crackrepair #concretecrackrepair #structuralreinforcementsolutions #contractors #engineering #solutions #commercialconstruction #commercialbuilding #parkinggarage #concretestrengthening #constructionerrors #products #engineering #support #buildingstrengthensuringstability