Parking garages are indispensable components of urban infrastructure, the importance of maintaining these structures cannot be overstated. By understanding the complexities of these structures and leveraging advanced materials and techniques, engineers can ensure that parking garages continue to serve their vital role in urban infrastructure safely and effectively.

Photo Courtesy of The Palm Beach Post
Surfside Condominium Parking Garage Collapse, Florida (2021)
On June 24, 2021, a section of the Champlain Towers South condominium in Surfside, Florida, collapsed. The failure initiated in the underground parking garage, leading to the collapse of a significant portion of the building above it.
Causes:
-
Structural Deterioration: Long-term exposure to saltwater intrusion caused concrete spalling and rebar corrosion in the parking garage.
-
Delayed Repairs: Despite previous warnings and inspection reports highlighting critical structural issues, necessary repairs were delayed.
Lessons Learned:
-
Timely Structural Assessments: Regular structural assessments and immediate action on identified issues are essential for building safety.
-
Addressing Environmental Factors: Structures in coastal areas require special attention to protect against saltwater intrusion and its damaging effects on concrete and steel.
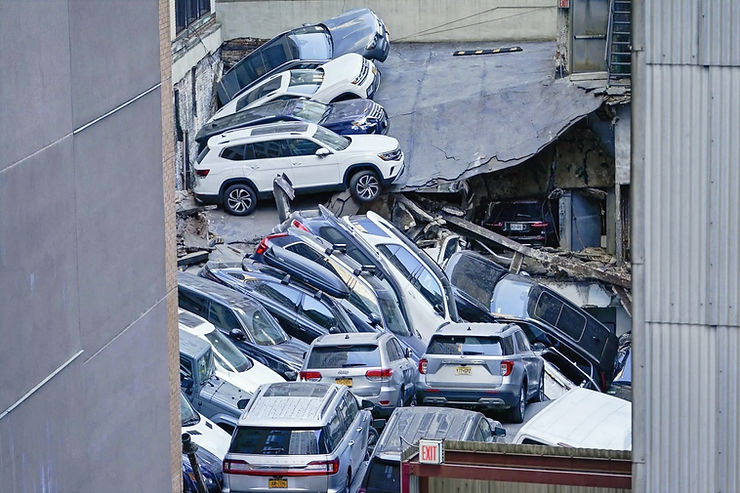
Photo Courtesy of AP News
Lower Manhattan Parking Garage Collapse, New York (2023)
On April 18, 2023, a parking garage in New York City experienced a catastrophic collapse, resulting in the structure's partial failure. The incident caused significant property damage, multiple injuries, and tragically, several fatalities.
Causes:
-
Structural Deficiencies: the parking garage collapse in New York on April 18, 2023, was primarily attributed to structural deficiencies exacerbated by overloading and inadequate maintenance.
Lessons Learned:
-
Proactive maintenance: The collapse underscored the critical importance of regular, thorough inspections and maintenance of parking structures. It highlighted the need for adherence to load capacity guidelines and the prompt addressing of any structural issues. The incident also emphasized the necessity of using modern reinforcement materials, such as carbon fiber, to strengthen aging infrastructures.
The growing adoption of electric vehicles


Electric Vehicles
3000-9000 lbs
Gas Vehicles
2500-6000 lbs
(EVs) present new challenges and considerations for the design, construction, and maintenance of parking garages. While EVs offer numerous environmental benefits, they also introduce additional loads and infrastructure requirements that parking garages must accommodate. Understanding these impacts is crucial for ensuring the safety, functionality, and longevity of parking structures.
Identifying warning signs of structural failure in parking garages





Key warning signs include visible cracks in concrete surfaces, spalling or flaking concrete, and water leaks or stains indicating potential water damage. Rust stains can signal corroding rebar within the concrete, while sagging or deflected beams and floors suggest compromised load-bearing capacity. Additionally, unusual vibrations or movements when vehicles traverse the garage, along with unusual noises such as creaking or popping, can indicate underlying structural problems. Regular inspections by qualified engineers are essential to detect these signs early and implement necessary repairs, ensuring the safety and longevity of the parking structure.
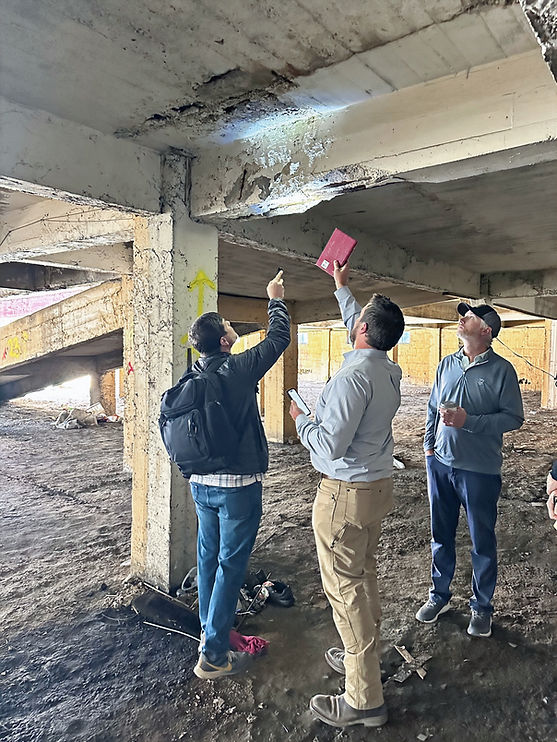
The role of carbon fiber in structural repairs
Carbon fiber can effectively repair critical areas of parking garages, such as concrete beams, columns, and slabs, by reinforcing and adding strength without adding significant weight.

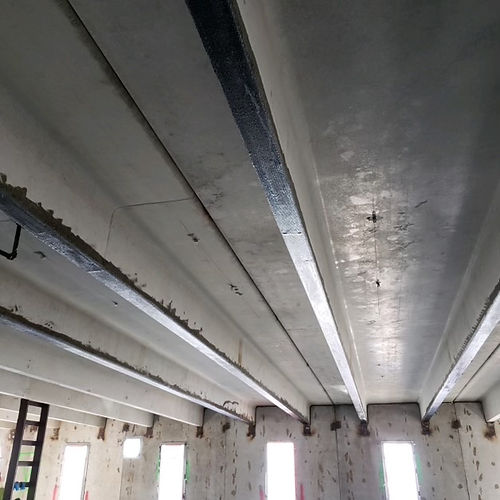


Identifying signs of structural failure and implementing effective carbon fiber solutions


Engineered for maximum safety & reliability

SRS offers comprehensive engineering support services tailored to ensure the structural integrity and safety of various infrastructures. Our expertise includes conducting detailed structural assessments, designing repair solutions, implementing advanced concrete-preserving products, and utilizing materials like carbon fiber for enhanced strength. SRS specializes in addressing critical issues in aging buildings and parking garages, providing maintenance recommendations and retrofitting strategies. Our skilled team of engineers collaborates closely with clients to deliver customized, effective solutions that meet regulatory standards and extend the lifespan of structures.

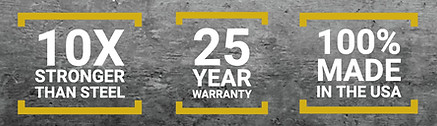
600 gsm unidirectional carbon fiber fabric designed to perform under pressure
A unidirectional, high-strength, non-corrosive carbon fiber fabric designed to be field laminated with SRS-1000 Epoxy adhesive to create a carbon fiber-reinforced polymer (CFRP) composite for structural reinforcement and strengthening of concrete and masonry structures.
660 gsm bi-directional carbon fiber fabric a high-performance, versatile solution
A bidirectional, high-strength, non-corrosive bidirectional carbon fiber fabric designed to be field laminated with SRS-1000 Epoxy adhesive to create a carbon fiber-reinforced polymer (CFRP) composite for structural reinforcement and strengthening of concrete and masonry structures.
Technical Data
Tested by Scientists, Trusted by Contractors, Approved by Engineers.

ICC-ES & AC125
Tested Systems
Engineer Approved
Specified Products
Experienced
Technical Support
Order Customization
Same Day Shipping
Why choose SRS?
We are the carbon fiber infrastructure rehabilitation experts. SRS proudly leads the way with American Made carbon fiber strengthening systems that are built around the needs of professionals, designed, and engineered to preserve concrete structural components.

A client experience you can rely on
Our expert in-house engineers and dedicated support team are committed to providing an unparalleled customer experience. With an extensive carbon fiber inventory and same day shipping, SRS has the materials and expertise you can count on.
• Engineered Carbon Fiber Designs
• Same Day Support
• Contractor Training
• Commercial Format Roll Kits